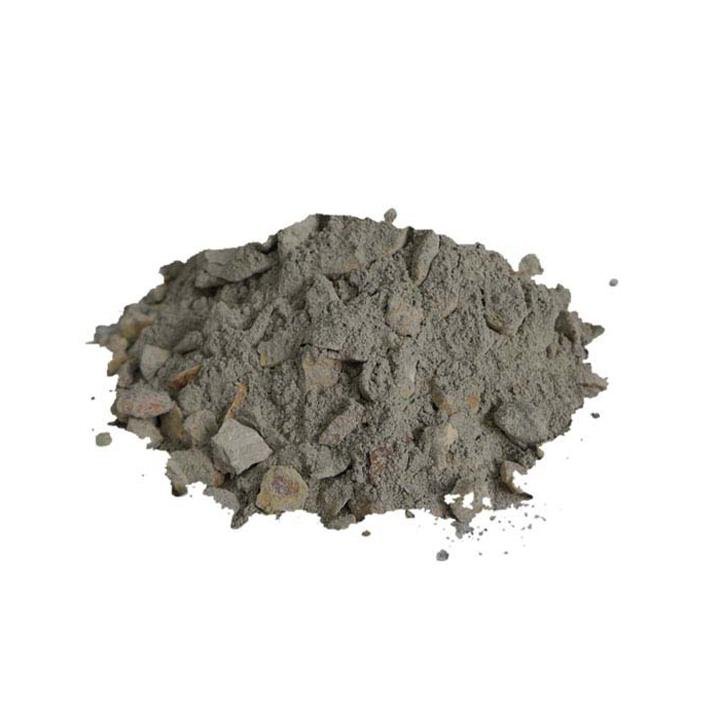
金屬鋁熔點相對不高,在660℃即可融化為鋁液,但其比熱容為0.88×103J/(Kg·℃),約為鐵的兩倍,因此鋁熔化過程中需要吸收更多的熱量,消耗更多的能量,鋁熔煉爐工作時熔體的溫度為700~800℃,在750℃時純鋁熔液的粘度約為0.104Pa·s,而水在20℃時粘度為0.1Pa·s,因此高溫鋁液具有粘度較低的特點,對耐火材料具有極強的滲透性。鋁的化學(xué)性質(zhì)活潑,能與爐內(nèi)氣體中的CO2、H2O、O2等發(fā)生反應(yīng),造成鋁的損失。鋁合金在高溫下容易與耐火爐襯中成分反應(yīng),生成新的產(chǎn)物并產(chǎn)生一定的體積變化,使耐火材料的結(jié)構(gòu)發(fā)生變化,改變材料的化學(xué)和物理性能,造成耐火材料的損毀。
而鋁熔液與耐火材料的接觸和浸潤是二者發(fā)生化學(xué)反應(yīng)的前提條件。因此,改善耐火材料的抗鋁液侵蝕性能的途徑有兩種,一是在耐火材料表面施加涂層;另外一種途徑是通過減少氣孔率、減小氣孔孔徑或增大熔體與材料的潤濕角來阻止其滲透。
通常通過以下措施來改善耐火材料的抗鋁液侵蝕性和潤濕性。
在原材料的選擇上偏向于與鋁溶液潤濕角小或相互之間不發(fā)生化學(xué)反應(yīng)的成分如Al2O3、SiC、Al4C3等為主要原材料,同時減少基質(zhì)中與鋁熔液反應(yīng)的的礦物成分,如石英和莫來石相等。一般來說,當(dāng)耐火材料和鋁熔液的潤濕角大于90°時兩者就呈不潤濕狀態(tài)。大部分的氧化物與鋁熔液的潤濕角都較小,且隨著溫度的升高或時間的延長,潤濕角會進一步減小,而碳化物、硼化物以及氮化物則不易與鋁熔液潤濕。有研究表明:700℃時的純鋁液與Al2O3材料的潤濕角為97°,與玻璃態(tài)碳的潤濕角為92°,與單晶和多晶石墨的潤濕角為126°,與單晶SiC的潤濕角為79°。也即在熔鋁爐的工作溫度下,鋁熔液與Al2O3材料和石墨材料不潤濕,但與SiC材料會潤濕。鋁熔煉爐的冶煉氣氛為氧化性氣氛,此時若采用石墨作為抗?jié)櫇駝?,及其容易因氧化而?dǎo)致失效。因此,提高耐火材料中的Al2O3含量相對來說可行。鋁合金熔液具有很強的滲透和侵蝕能力,僅僅依靠調(diào)整礦物組成,不能從根本上改善材料的抗鋁熔液侵蝕性能。降低材料的顯氣孔率以及減小材料的氣孔孔徑可以減少鋁熔液的滲入通道,增大熔液向耐材中滲透的阻力。采用合適的顆粒級配,引入微粉,以及采用高效的分散技術(shù),都可以降低材料的顯氣孔率。在實際操作中一般采用Andreassen緊密堆積原理作為耐火澆注料理論指導(dǎo),盡可能逼近佳顆粒級配;在澆注料中加入適量的α-Al2O3微粉和SiO2微粉等,在燒結(jié)后填充于基質(zhì)中間的小空隙內(nèi),以此降低材料的顯氣孔率,但微粉及超微粉容易團聚,因此通常加入高效分散劑,使微粉在材料中可以充分均勻。添加抗鋁液潤濕劑可以降低鋁熔液與耐火材料間的潤濕性或減小材料的顯氣孔率,從而阻止鋁熔液和材料之間的反應(yīng),抗鋁液潤濕劑主要的作用機理是與材料組份發(fā)生反應(yīng)或填充于空隙中或與鋁液具有較大的潤濕角,此部分工作研究人員已經(jīng)有了長足的進展,效果相對較好的抗鋁液潤濕劑主要有:BaSO4、Na3AlF6、CaSO4、CaF2、Cr2O3、Si3N4、AlF3、P2O5、TiB2、SrTiO3等。涂層的存在可以隔絕或很大程度上減少材料與熔體的接觸,但涂層應(yīng)具備耐高溫及不與熔體浸潤的特點,采用氮化物、硼化物等組份制備可與材料形成牢固結(jié)合的涂層是一條良好的途徑,但此部分研究由于采用特定材料及提高工藝水平已可以滿足使用需求而很少研究。